Podstawy sleevowania
Czym jest sleevowanie?
Sleevowanie (ang. sleeving) to proces aplikowania elastycznej etykiety w postaci rękawa (tzw. sleeve), który zostaje obkurczony lub naciągnięty wokół opakowania w celu uzyskania idealnie dopasowanej etykiety o wysokich walorach wizualnych i użytkowych. Technologia ta jest powszechnie stosowana w wielu branżach – od spożywczej, przez kosmetyczną i farmaceutyczną, po chemiczną i przemysłową.
Krótka historia sleevowania
Choć sama idea etykietowania opakowań ma wielowiekową tradycję, sleevowanie narodziło się wraz z rozwojem polimerów i technologii folii termokurczliwych w XX wieku. Początkowo wykorzystywano je głównie w obszarach wymagających wyraźnego oznaczenia produktów (np. branża spożywcza). Z czasem, dzięki udoskonaleniom w produkcji folii, drukowaniu (flexo, rotograwiura) oraz automatyzacji linii, sleevowanie zyskało na popularności, stając się jedną z najważniejszych metod etykietowania.
Podstawowe pojęcia związane z technologią sleevowania
- Sleeve – etykieta w formie rurki z folii termokurczliwej (np. PET, OPS, PVC) lub stretch sleeve (bez konieczności obkurczania).
- Tunel obkurczający – urządzenie wykorzystujące gorące powietrze, parę wodną lub promienniki podczerwieni do obkurczenia etykiety na opakowaniu.
- Aplikator (sleever) – maszyna nakładająca sleeve na opakowanie przed procesem obkurczania (lub jedyna maszyna w przypadku stretch sleeve).
- Tamper-evident – funkcjonalność zapewniająca dodatkowe zabezpieczenie produktu przed nieautoryzowanym otwarciem (np. w formie „plomby” z folii na szyjce butelki).
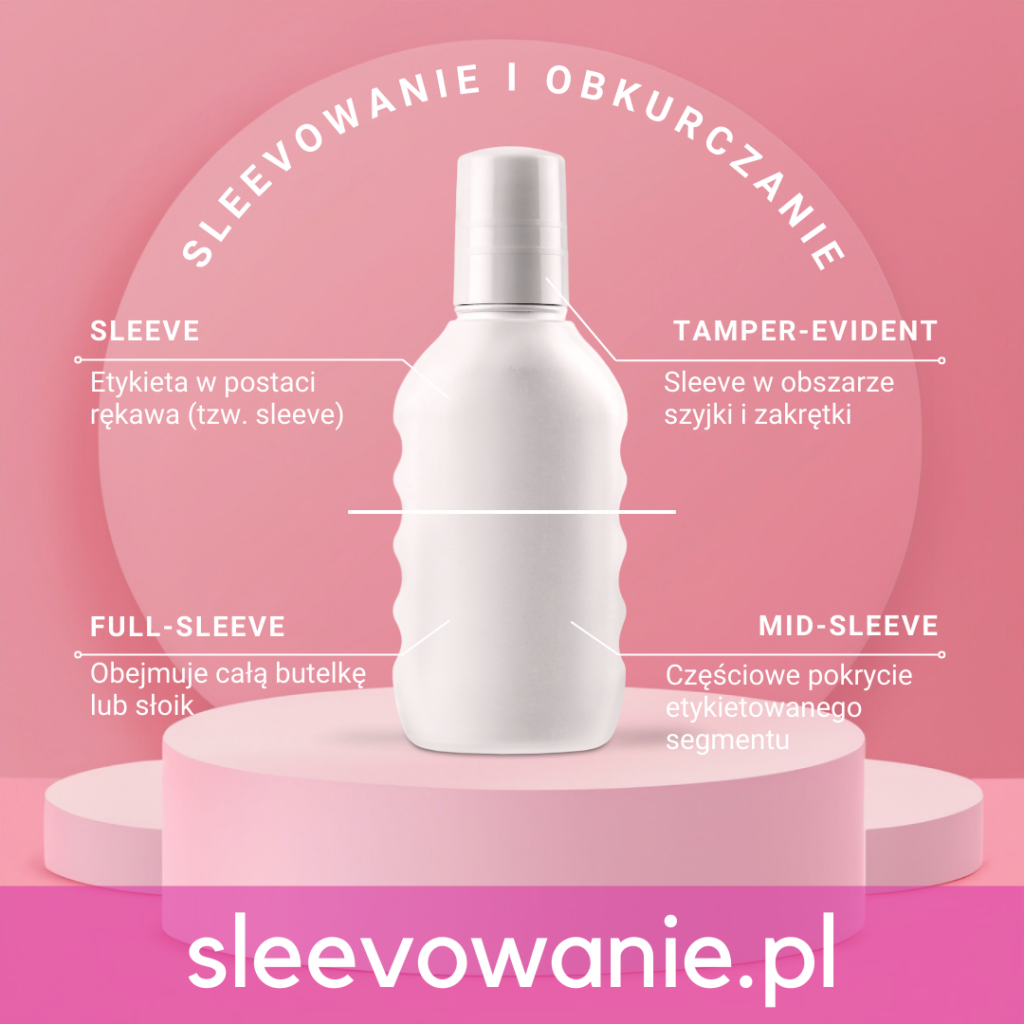
Różnice między sleevowaniem a tradycyjnymi metodami etykietowania
Tradycyjne metody etykietowania
- Etykiety samoprzylepne (pressure-sensitive labels): naklejane na powierzchnię opakowania, zazwyczaj na ograniczonym fragmencie.
- Etykiety klejone na mokro (wet glue labels): stosowane w branży napojów, gdzie etykieta pokrywana jest warstwą kleju przy aplikacji.
- In-Mold Labeling (IML): łączenie etykiety z opakowaniem już na etapie formowania (np. wtrysku tworzywa), co daje bardzo trwały efekt, ale jest kosztowne i wymaga odpowiednio przygotowanych form.
Sleevowanie
- Zakrycie całego opakowania lub wybranego fragmentu (np. szyjka butelki), co pozwala na tworzenie efektownych projektów graficznych 360°.
- Możliwość szybkiej zmiany designu poprzez wymianę rękawa foliowego, bez konieczności modyfikacji form czy kształtu opakowania.
- Zastosowanie funkcjonalnych rozwiązań (np. tamper-evident, perforacje ułatwiające otwarcie, dodatkowa ochrona przed promieniowaniem UV).
- Proces obkurczania pozwala na precyzyjne dopasowanie etykiety do nawet najbardziej nieregularnych kształtów butelek, słoików czy puszek.
Zalety sleevowania
- Pełna powierzchnia reklamy (360°) – zwiększa atrakcyjność wizualną produktu i pozwala na zamieszczenie większej ilości informacji.
- Doskonała ochrona nadruku – grafika i dane są odporne na ścieranie czy wilgoć, ponieważ znajdują się w warstwie wewnętrznej folii.
- Łatwe dostosowanie do różnych kształtów – etykieta idealnie przylega do produktu po procesie obkurczania, bez zagnieceń i pęcherzyków powietrza.
- Funkcje zabezpieczające – tamper-evident, perforacje do wygodnego otwierania, możliwość użycia folii barierowych.
- Elastyczność i szybka modyfikacja designu – wystarczy zmienić projekt nadruku i zamówić nowe sleeve’y, bez potrzeby skomplikowanej modyfikacji linii produkcyjnej.
Gdzie dokładnie aplikowany jest rękaw sleeve?
Sleeve może zostać umieszczony na różne sposoby, w zależności od potrzeb producenta oraz rodzaju opakowania:
- Pełna powierzchnia opakowania – obejmuje całą butelkę lub słoik od podstawy aż po szyjkę lub nakrętkę. Tego typu zastosowanie pozwala na maksymalne wyeksponowanie grafiki, oferując etykietę w 360°, przyciągając wzrok i wyróżniając produkt na półce.
- Częściowe pokrycie – np. od określonego punktu na butelce (mid-sleeve), tylko wokół etykietowanego segmentu lub w strefie promocji. Ta opcja zapewnia większą kontrolę kosztów materiałowych i mniejsze zużycie folii.
- Obszar szyjki i zakrętki (tamper-evident) – rękaw nakładany wyłącznie na górną część opakowania, by stanowić zabezpieczenie przed nieuprawnionym otwarciem (tzw. banderola bezpieczeństwa). Często stosowany w branży napojów, kosmetykach czy w farmacji.
- Połączenie szyjki z głównym korpusem – czasami etykieta tworzona jest w dwóch częściach: główna część obejmuje korpus opakowania, a dodatkowy fragment na szyjce pełni funkcję zabezpieczenia (tamper-evident). Obie sekcje mogą być ułożone w jednym kawałku folii, a później obkurczone.
Przykłady zastosowań
- Branża spożywcza: butelki z napojami, opakowania jogurtów, sosów, konserw.
- Kosmetyki: opakowania dezodorantów, kremów czy szamponów o nietypowych kształtach.
- Farmacja: fiolki, słoiki, buteleczki z lekami, które wymagają dodatkowego zabezpieczenia (tamper-evident).
- Chemia gospodarcza: detergenty w różnorodnych kształtach butelek.
Sleevowanie wyróżnia się wszechstronnością, estetyką i możliwością zabezpieczenia produktu, co czyni je coraz częstszym wyborem w nowoczesnych liniach pakujących. Mimo wyższych kosztów inwestycyjnych i materiałowych, firmy decydują się na tę technologię, aby uzyskać efektowne i bezpieczne opakowanie, które przyciąga wzrok na sklepowej półce.
Skontaktuj się z nami pod adresem kontakt@bovmatic.pl lub numerem 605 318 315, aby dowiedzieć się więcej o naszych usługach i produktach oferowanych przez naszą firmę i naszych Partnerów.
Obkurczanie sleeve
Obkurczanie sleeve to kluczowy etap w procesie nakładania etykiet typu sleeve na butelki, słoiki czy inne kształty opakowań. Pozwala on na idealne dopasowanie folii do produktu i uzyskanie atrakcyjnego efektu wizualnego w postaci zadrukowanego „rękawa” obejmującego cały lub wybrany fragment opakowania. Poniżej znajdziesz przegląd najważniejszych aspektów związanych z obkurczaniem.
1. Cel i znaczenie procesu obkurczania
- Perfekcyjne przyleganie: dzięki odpowiedniej temperaturze oraz ciśnieniu (gorące powietrze, para wodna lub promienniki IR) folia obkurcza się i dopasowuje do nawet najbardziej skomplikowanych kształtów opakowań.
- Walory estetyczne: proces obkurczania umożliwia wyeksponowanie pełnej grafiki 360°, co przekłada się na większą atrakcyjność produktu na półce.
- Zabezpieczenie: w przypadku funkcji tamper-evident (plomba na szyjce czy nakrętce) obkurczenie folii stanowi dodatkowe zabezpieczenie przed otwarciem, gwarantując higienę i autentyczność produktu.
2. Rodzaje tuneli obkurczających
- Tunel powietrzny (hot air)
- Źródło ciepła: nagrzane powietrze, kierowane na powierzchnię folii przez specjalne dysze.
- Zastosowanie: szeroki zakres produktów i prędkości linii, sprawdza się w wielu gałęziach przemysłu (spożywczy, kosmetyczny, chemiczny).
- Zalety: relatywnie łatwa kontrola temperatury i kierunku nadmuchu.
- Tunel parowy (steam tunnel)
- Źródło ciepła: nasycona para wodna.
- Zastosowanie: szczególnie efektywny przy opakowaniach o nieregularnym kształcie oraz tam, gdzie wymagana jest bardzo wysoka precyzja i równomierne obkurczanie.
- Zalety: para wodna dobrze rozprowadza ciepło, minimalizując ryzyko fałdowania się etykiety.
- Tunel z promiennikami IR (podczerwieni)
- Źródło ciepła: promienniki podczerwieni kierowane na etykietę.
- Zastosowanie: często łączony z innymi typami tuneli w celu szybszego, wstępnego obkurczenia.
- Zalety: bardzo szybkie podgrzanie wybranych obszarów, co bywa pomocne przy kształtach opakowań trudnych do równomiernego nagrzania samym powietrzem czy parą.
Wybór typu tunelu zależy od wymagań produkcyjnych, rodzaju zastosowanej folii (PET, OPS, PVC itp.), a także kształtu opakowania i oczekiwanej prędkości linii pakującej.
3. Przebieg procesu obkurczania
- Nakładanie folii (sleever)
- Na opakowanie (butelkę, słoik) nakładany jest rękaw z folii (tzw. sleeve).
- Proces ten odbywa się zwykle poprzez automatyczny aplikator, który tnie folię z rolki i zsuwa ją na opakowanie.
- Transport do tunelu
- Opakowania przesuwają się na taśmie transportowej do tunelu obkurczającego.
- Stabilizacja butelki/słoika w tunelu często odbywa się za pomocą prowadnic bocznych, które utrzymują opakowanie we właściwej pozycji.
- Obkurczanie właściwe
- W tunelu następuje ekspozycja rękawa na gorące powietrze, parę lub promieniowanie IR, co powoduje dopasowanie etykiety do konturów opakowania.
- Istotne jest precyzyjne ustawienie parametrów (temperatura, czas, prędkość transportu, siła nadmuchu/pary), aby uniknąć przegrzania lub niedostatecznego obkurczenia.
- Studzenie i kontrola jakości
- Po wyjściu z tunelu folia szybko się wychładza, stabilizując się na powierzchni opakowania.
- Następnie opakowanie może być kierowane do kontroli jakości (m.in. sprawdzenie poprawności nadruku, wystąpienia ewentualnych fałd czy pęcherzyków powietrza).
4. Kluczowe czynniki wpływające na jakość obkurczania
- Rodzaj folii
- PET, OPS, PVC – każdy materiał wymaga innych parametrów procesu (różna temperatura topnienia i kurczenia).
- Grubość folii wpływa na prędkość obkurczania i trwałość etykiety.
- Temperatura i czas
- Zbyt niska temperatura lub zbyt krótki czas ekspozycji mogą spowodować niedokładne dopasowanie etykiety.
- Przegrzanie folii może skutkować zniekształceniami grafiki lub nawet jej przetapianiem.
- Prędkość transportu
- Utrzymanie stabilnej prędkości linii umożliwia jednolite obkurczenie kolejnych opakowań, co przekłada się na spójność wizualną końcowych produktów.
- Równomierny nadmuch
- W przypadku tunelu z gorącym powietrzem istotny jest jednolity rozkład strumienia ciepła (układ dysz, intensywność nadmuchu).
- W przypadku pary – równa dystrybucja pary wodnej po całym obwodzie etykiety.
5. Kontrola jakości i najczęstsze problemy
- Fałdy i pofałdowania: mogą wynikać z nierównomiernego rozkładu ciepła lub nieodpowiedniej synchronizacji prędkości taśmy z temperaturą.
- Nierówna grafika: zbyt gwałtowny proces obkurczania potrafi zdeformować nadruk, zwłaszcza przy niestandardowych kształtach opakowań.
- Niedokładne wykończenie przy szyjce/opasce zabezpieczającej: wymaga precyzyjnego doboru parametrów zwłaszcza w strefie tzw. tamper-evident.
Aby zapobiec tym błędom, stosuje się systemy wizyjne, czujniki temperatury oraz automatyczne regulatory prędkości przesuwu taśmy. Dzięki temu możliwe jest bieżące dostosowanie procesu do zmiennych warunków (np. wahania temperatury otoczenia, inne typy opakowań).
6. Zalety obkurczania w kontekście sleevowania
- Precyzyjne dopasowanie do kształtu opakowania – nawet w przypadku niestandardowych projektów.
- Ochrona nadruku przed ścieraniem się i wpływem wilgoci, ponieważ nadruk znajduje się wewnętrznej warstwie folii.
- Możliwość tworzenia efektów specjalnych (np. elementy matowe, błyszczące, transparentne), poprawiających atrakcyjność produktu.
- Elastyczność – w razie potrzeby łatwo zmienić projekt graficzny i zamówić nowe rękawy, bez konieczności przebudowy linii produkcyjnej.
Skontaktuj się z nami
Obkurczanie sleeve to serce procesu etykietowania termokurczliwego, wpływające na końcowy wygląd i jakość produktu. Dobór odpowiedniego tunelu (powietrznego, parowego, IR), parametrów cieplnych i rodzaju folii decyduje o tym, czy opakowanie zyska profesjonalny, przyciągający wzrok wygląd. Dzięki dynamicznemu rozwojowi technologii, współczesne linie do sleevowania oferują wysoką wydajność, precyzję i niezawodność, czyniąc sleeve jedną z wiodących metod etykietowania na rynku.
Skontaktuj się z nami pod adresem kontakt@bovmatic.pl lub numerem 605 318 315, aby dowiedzieć się więcej o naszych usługach i produktach oferowanych przez naszą firmę i naszych Partnerów.
Aplikator sleeve
Aplikator sleeve – często określany również mianem sleevera – to kluczowy element w procesie nakładania etykiet termokurczliwych (tzw. sleeve) na opakowania. Dzięki niemu możliwe jest precyzyjne i wydajne umieszczenie etykiety w formie rękawa na butelce, słoiku czy pojemniku przed etapem obkurczania. Poniżej przedstawiamy najważniejsze aspekty dotyczące budowy, działania i zastosowania aplikatorów sleeve w nowoczesnych liniach produkcyjnych.
1. Rola aplikatora w procesie sleevowania
- Przygotowanie etykiety (rękawa)
- Aplikator odcina odpowiedni fragment folii z roli (tzw. sleeve roll) i otwiera go, tworząc kształt rurki.
- W niektórych systemach możliwe jest także wycięcie perforacji lub nacięcia (np. do funkcji tamper-evident).
- Nakładanie rękawa na opakowanie
- Rękaw zostaje zsunięty na butelkę, słoik czy inny kształt opakowania.
- Kluczowe jest precyzyjne centrowanie – zapewnia to właściwe ułożenie etykiety względem powierzchni opakowania i przyszły prawidłowy obkurcz (bez fałd i zagnieceń).
- Kontrola i przejście do tunelu obkurczającego
- Po nałożeniu rękawa opakowanie trafia do sekcji obkurczania (tunel gorącego powietrza, parowy lub IR), gdzie następuje finalne dopasowanie etykiety.
2. Budowa i zasada działania aplikatora sleeve
- Zespół odwijania folii
- Rolka z nadrukowaną folią sleeve umieszczana jest na osi podawczej.
- Układ prowadnic i czujników dba o płynny transport folii, zapobiegając jej zaginaniu czy nadmiernemu naprężaniu.
- Mechanizm cięcia
- Specjalne noże rotacyjne, ultradźwiękowe lub termiczne dokonują precyzyjnego rozdzielenia folii na odcinki odpowiadające wysokości opakowania.
- Ważne, aby cięcie było idealnie proste, co gwarantuje późniejsze równe obkurczenie etykiety.
- Część formująca (tubing)
- Folia jest formowana w kształt rurki i utrzymywana w takiej formie do momentu nałożenia na opakowanie.
- System prowadnic i rolek dystansujących dba o brak fałd i utrzymanie folii w odpowiednim położeniu.
- Głowica nakładająca (aplikator właściwy)
- Urządzenie zsuwa powstały „rękaw” na opakowanie, np. przy pomocy chwytaków, kołnierzy przesuwających lub ruchu pneumatycznego.
- Dokładność tej operacji decyduje o efekcie końcowym – etykieta musi znaleźć się w ściśle określonej pozycji.
- System sterowania i kontroli
- Nowoczesne aplikatory sleeve są wyposażone w panele dotykowe, czujniki obecności i kamery wizyjne, które pozwalają na bieżąco monitorować proces i minimalizować ryzyko błędów.
3. Rodzaje aplikatorów sleeve
- Aplikatory liniowe
- Opakowania przesuwają się w jednym rzędzie na taśmie transportowej.
- Rozwiązanie często stosowane w średnich i dużych liniach produkcyjnych, zapewniające wysoką wydajność.
- Aplikatory rotacyjne
- Opakowania są przemieszczane wokół centralnego osiowego mechanizmu, co umożliwia szybszą aplikację i dokładniejsze pozycjonowanie etykiet.
- Zwykle spotykane w instalacjach o bardzo wysokiej wydajności, np. w branży napojów.
- Aplikatory kompaktowe (stołowe)
- Dedykowane dla mniejszych linii lub produkcji warsztatowej, gdzie przestrzeń jest ograniczona.
- Pomimo kompaktowych rozmiarów mogą osiągać zadowalającą precyzję i efektywność w mniejszych nakładach produkcyjnych.
4. Parametry kluczowe
- Prędkość aplikacji
- Wyrażana w opakowaniach na minutę (ppm). Topowe modele osiągają do kilkuset opakowań/min, co sprawdza się w dużych fabrykach.
- Zakres wymiarów etykiet i opakowań
- Każdy aplikator ma określony maksymalny i minimalny obwód oraz wysokość etykiety, jaką potrafi obsłużyć.
- Typ obsługiwanej folii
- PET, OPS, PVC, a także różne grubości (zazwyczaj 40–70 mikronów). Niektóre urządzenia obsługują też folie ekologiczne (np. PLA).
- Opcje dodatkowe
- Tamper-evident (banderole bezpieczeństwa), perforacje ułatwiające otwieranie, możliwość nakładania sleeve’a tylko na część opakowania (tzw. partial sleeving).
5. Korzyści z zastosowania aplikatorów sleeve
- Zautomatyzowanie procesu
- Redukcja kosztów pracy ręcznej i ryzyka błędów związanych z ręcznym etykietowaniem.
- Wysoka jakość i powtarzalność
- Precyzyjne centrowanie i stabilne nakładanie etykiety gwarantują spójny wygląd każdego produktu.
- Elastyczność
- Możliwość szybkiej zmiany rodzaju i rozmiaru etykiety w zależności od potrzeb rynku oraz kampanii marketingowych.
- Kompatybilność z systemami kontroli
- Możliwość integracji z kamerami wizyjnymi, sensorami, a także łączenia z innymi maszynami (np. dozownikami, zakręcarkami, owijarkami) w ramach kompleksowej linii produkcyjnej.
6. Przykładowe zastosowania aplikatorów sleeve
- Branża spożywcza: nakładanie kolorowych, całopowierzchniowych etykiet na butelki z sokami, napojami gazowanymi czy mlecznymi.
- Branża kosmetyczna: eleganckie opakowania z folii matowej, połyskującej lub przezroczystej, zapewniające unikalny design i doskonałą ochronę przed wilgocią.
- Farmacja i chemia: systemy tamper-evident, chroniące produkty przed ingerencją.
- Przemysł premium: luksusowe, wielokolorowe efekty w 360°, pozwalające na wyróżnienie marki na półce sklepowej.
Skontaktuj się z nami
Aplikator sleeve stanowi fundament procesu etykietowania termokurczliwego, gwarantując stabilność, precyzję i wysoką wydajność. Dzięki odpowiedniemu doborowi rodzaju aplikatora (liniowy, rotacyjny, kompaktowy) i kompatybilności z tunelami obkurczającymi możliwe jest stworzenie w pełni zautomatyzowanej linii produkcyjnej, dostosowanej do potrzeb konkretnej branży. Efekt? Doskonale wyeksponowany produkt, zabezpieczony i wyróżniający się na rynku.
Skontaktuj się z nami pod adresem kontakt@bovmatic.pl lub numerem 605 318 315, aby dowiedzieć się więcej o naszych usługach i produktach oferowanych przez naszą firmę i naszych Partnerów.
Parowy tunel obkurczający
Parowy tunel obkurczający to jedno z najskuteczniejszych rozwiązań w procesie etykietowania termokurczliwego (tzw. sleevowania). Dzięki wykorzystaniu nasyconej pary wodnej, tunel zapewnia niezwykle precyzyjne i równomierne obkurczanie etykiet (tzw. sleeve) wokół opakowań o nawet najbardziej złożonych kształtach. W poniższym artykule przybliżamy główne cechy, zalety i zastosowania parowych tuneli obkurczających w nowoczesnych liniach pakujących.
1. Charakterystyka parowego tunelu obkurczającego
- Źródło ciepła: para wodna
W przeciwieństwie do tuneli z gorącym powietrzem czy promiennikami podczerwieni (IR), parowy tunel obkurczający wykorzystuje nasyconą parę wodną, która otacza etykietę i równomiernie przekazuje energię cieplną na całą jej powierzchnię. - Kontrola temperatury i wilgotności
Nowoczesne systemy parowe umożliwiają dokładną regulację parametrów (ciśnienie, temperatura, natężenie przepływu pary), co przekłada się na stabilną pracę tunelu i minimalizuje ryzyko przegrzania lub niedokładnego obkurczania. - Budowa i sekcje grzewcze
Wiele tuneli parowych dzieli się na sekcje (moduły), w których para jest dozowana pod różnym kątem i z różną intensywnością. Pozwala to na dostosowanie procesu do indywidualnych kształtów butelek, słoików czy puszek.
2. Przebieg procesu obkurczania w tunelu parowym
- Wprowadzenie opakowań
Butelki, słoiki lub inne pojemniki, już z zaaplikowaną etykietą w formie rękawa (sleeve), trafiają na taśmę transportową tunelu. - Ekspozycja na parę wodną
Wewnątrz tunelu opakowania są równomiernie otaczane nasyconą parą. Dzięki temu etykieta ulega szybkiemu i dokładnemu obkurczeniu, dopasowując się do konturów opakowania. - Chłodzenie i stabilizacja
Po wyjściu z tunelu etykieta szybko się wychładza i utrwala. Opakowania kierowane są następnie do dalszych etapów procesu (np. kontroli jakości, pakowania zbiorczego).
3. Główne zalety parowego tunelu obkurczającego
- Równomierne obkurczanie
Para wodna otacza całe opakowanie, co pozwala na precyzyjne dopasowanie etykiety do jego kształtu – bez fałd, zagięć czy zniekształceń nadruku. Jest to szczególnie istotne przy opakowaniach o nieregularnych formach. - Wysoka wydajność
Tunel parowy osiąga dużą szybkość obkurczania przy jednoczesnym zachowaniu stabilności procesu. Dzięki temu świetnie sprawdza się w liniach o wysokiej przepustowości (np. branża napojów, kosmetyki, chemia gospodarcza). - Elastyczność
Możliwość precyzyjnej regulacji parametrów takich jak ciśnienie czy natężenie przepływu pary ułatwia dostosowanie tunelu do różnych rodzajów folii termokurczliwych (PET, OPS, PVC itp.) i różnorodnych kształtów opakowań. - Mniejsze ryzyko przegrzania folii
Dzięki dobrym właściwościom wymiany ciepła para szybciej i bardziej równomiernie nagrzewa etykietę niż gorące powietrze, co pozwala na redukcję wad produkcyjnych związanych z lokalnym przegrzaniem (np. marszczeniem czy deformacją nadruku). - Wszechstronność
Parowe tunele obkurczające są często modulowe i dają się łatwo integrować z aplikatorami etykiet, inspektorami wizyjnymi czy systemami pakowania zbiorczego, tworząc kompletne linie produkcyjne.
4. Kryteria wyboru tunelu parowego
- Wielkość i przepustowość linii
Przy dużych zakładach produkcyjnych kluczowa będzie wydajność i możliwość integracji tunelu z istniejącymi maszynami. W mniejszych firmach znaczenie mogą mieć kompaktowe wymiary lub łatwość przenoszenia urządzenia. - Rodzaj produktu i kształt opakowania
Tunel parowy doskonale sprawdza się przy opakowaniach o skomplikowanej geometrii, gdzie równomierne obkurczenie standardowymi metodami byłoby trudniejsze. - Oczekiwana jakość nadruku
Jeśli priorytetem jest doskonałe zachowanie szczegółów grafiki na całej powierzchni etykiety, parowy tunel będzie optymalnym wyborem ze względu na stabilny i równomierny rozkład ciepła. - Typ folii
Warto upewnić się, czy tunel jest przystosowany do materiału, z którego wykonane są etykiety (różne folie mogą wymagać innych parametrów temperaturowych lub poziomu wilgotności).
5. Zastosowanie w różnych branżach
- Branża spożywcza: obkurczanie etykiet na butelkach z sokami, napojami gazowanymi, wodą oraz opakowaniach żywności (jogurty, sery, przetwory).
- Przemysł kosmetyczny: etykiety na flakonach perfum, dezodorantach, kremach – szczególnie istotne jest precyzyjne obkurczenie, by nie zakłócać estetyki produktu.
- Farmacja: tamper-evident sleeve na butelkach z syropami, fiolkach i słoiczkach, gdzie higiena i szczelność mają kluczowe znaczenie.
- Chemia gospodarcza: detergenty, środki czystości w nietypowych butelkach o nieregularnych kształtach.
6. Konserwacja i eksploatacja tunelu parowego
- Czyszczenie i odprowadzanie kondensatu: w tunelu gromadzi się para, która skrapla się w postaci wody. Niezbędny jest więc odpowiednio zaprojektowany system odprowadzania kondensatu, a także regularne mycie i konserwacja elementów stykających się z parą.
- Monitoring parametrów: nowoczesne tunele posiadają sensory temperatury, czujniki ciśnienia i panele sterowania umożliwiające dostosowanie ustawień w czasie rzeczywistym.
- Bezpieczeństwo: ze względu na pracę w wysokiej temperaturze należy zwrócić uwagę na systemy zabezpieczające (m.in. awaryjne wyłączenie, barierki ochronne, izolację termiczną).
Skontaktuj się z nami
Parowy tunel obkurczający oferuje wyjątkową precyzję i efektywność w procesie sleevowania, szczególnie w przypadku wymagających projektów i niestandardowych kształtów opakowań. Równomierna dystrybucja ciepła, szybkie dopasowanie folii oraz elastyczność ustawień sprawiają, że jest to jedno z najbardziej cenionych rozwiązań w branży opakowań. Dzięki tunelom parowym producenci mogą uzyskać doskonały efekt wizualny, co przekłada się na wyższą konkurencyjność i lepszą rozpoznawalność marki na rynku.
Skontaktuj się z nami pod adresem kontakt@bovmatic.pl lub numerem 605 318 315, aby dowiedzieć się więcej o naszych usługach i produktach oferowanych przez naszą firmę i naszych Partnerów.
Obkurczarki etykiet sleeve
Obkurczarki etykiet sleeve to urządzenia kluczowe dla finalnego etapu sleevowania – procesu, w którym etykieta w formie elastycznego rękawa (tzw. sleeve) zostaje obkurczona wokół opakowania. Dzięki temu etykieta idealnie przylega do nawet najbardziej nietypowych kształtów butelek, słoików czy pojemników. Poniżej przedstawiamy przegląd rodzajów obkurczarek, zasady ich działania oraz najważniejsze korzyści płynące z ich zastosowania.
1. Czym są obkurczarki etykiet sleeve?
Obkurczarki etykiet sleeve to urządzenia, w których odpowiednio przygotowana folia (np. PET, OPS, PVC) zostaje poddana działaniu wysokiej temperatury (gorącego powietrza, pary wodnej lub promieni podczerwonych). W efekcie następuje równomierne dopasowanie etykiety do powierzchni opakowania, podkreślając jego kształt i zapewniając pełne (360°) pokrycie grafiki.
2. Rodzaje obkurczarek etykiet sleeve
- Obkurczarki z gorącym powietrzem (hot air)
- Zasada działania: strumień rozgrzanego powietrza kierowany jest na powierzchnię etykiety za pomocą specjalnych dysz.
- Zastosowanie: uniwersalne rozwiązanie dla szerokiej gamy opakowań o średnim i wyższym wolumenie produkcyjnym.
- Zalety: łatwość konfiguracji, stosunkowo niski koszt inwestycji, możliwość dopasowania nadmuchu do różnych kształtów.
- Obkurczarki parowe (steam tunnels)
- Zasada działania: etykieta poddawana jest działaniu nasyconej pary wodnej, która obkurcza folię, precyzyjnie dopasowując ją do opakowania.
- Zastosowanie: idealne przy nieregularnych, skomplikowanych kształtach, szczególnie w branży spożywczej (butelki, puszki, pojemniki o fantazyjnych konturach).
- Zalety: równomierna dystrybucja ciepła, mniejsze ryzyko miejscowego przegrzania folii, wysoka jakość obkurczenia.
- Obkurczarki wykorzystujące promienniki IR (podczerwień)
- Zasada działania: promienniki IR emitują fale, które podgrzewają folię w krótkim czasie, co pozwala na jej szybkie obkurczenie.
- Zastosowanie: często łączone z innymi metodami (np. tunel powietrzny) w celu zwiększenia wydajności lub wstępnego obkurczania określonych fragmentów etykiety.
- Zalety: szybki transfer ciepła, możliwość precyzyjnego nakierowania promienników na wybrane obszary.
- Rozwiązania hybrydowe
- Zasada działania: łączą w sobie elementy gorącego powietrza, pary lub IR w jednym tunelu, umożliwiając płynną regulację i dostosowanie do różnych rodzajów folii i kształtów opakowań.
- Zastosowanie: linie produkcyjne, gdzie wymagana jest maksymalna elastyczność – np. różnorodna gama produktów na jednej linii.
- Zalety: wysoka uniwersalność, zoptymalizowana wydajność, mniejsze ryzyko przestojów związanych z przezbrojeniem.
3. Kluczowe parametry i etapy działania obkurczarek
- Regulacja temperatury
- Niezwykle ważne, aby parametry cieplne były dostosowane do rodzaju folii – zbyt wysoka temperatura może spowodować zniekształcenie nadruku lub rozerwanie etykiety, zbyt niska – niedokładne obkurczenie.
- Prędkość transportu opakowań
- Linia transportująca musi być zsynchronizowana z czasem ekspozycji etykiety na źródło ciepła (powietrze, para, IR).
- Zbyt szybki przesuw może skutkować niedokładnym obkurczeniem, a zbyt wolny – przegrzaniem folii.
- Kontrola przepływu powietrza/strumienia pary
- W przypadku obkurczarek z gorącym powietrzem i parowych kluczowy jest równomierny rozkład temperatury wewnątrz komory.
- Zaawansowane systemy dysz i modułów sterujących pozwalają na dostosowywanie strumienia do konkretnych obszarów opakowania.
- Stabilizacja opakowania
- Podczas obkurczania butelki lub słoiki mogą wymagać prowadnic bocznych lub dodatkowych uchwytów, aby uniknąć przesunięć i zapewnić perfekcyjne wykończenie etykiety.
4. Zalety stosowania obkurczarek etykiet sleeve
- Estetyka i marketing
- Etykiety termokurczliwe zapewniają pełne pokrycie 360°, przyciągając wzrok konsumentów i umożliwiając kreatywne projekty graficzne.
- Zabezpieczenie produktu
- Obkurczone etykiety mogą pełnić funkcję tamper-evident (zabezpieczenie przed nieautoryzowanym otwarciem), wzmacniając zaufanie klienta do marki.
- Trwałość i odporność
- Ochrona etykiety przed ścieraniem, wilgocią czy uszkodzeniami mechanicznymi, dzięki folii pokrywającej całe opakowanie.
- Uniwersalność
- Możliwość zastosowania na różnorodnych kształtach i wymiarach opakowań, co sprzyja optymalizacji procesu pakowania w wielu gałęziach przemysłu (spożywczy, kosmetyczny, farmaceutyczny, chemiczny).
- Wysoka wydajność
- Obkurczarki etykiet sleeve doskonale integrują się w liniach produkcyjnych o dużej przepustowości, gwarantując maksymalną efektywność i niskie koszty jednostkowe.
5. Zastosowanie w różnych branżach
- Branża spożywcza: butelki z napojami, puszki, jogurty, sery czy słoiki z przetworami wymagające atrakcyjnej i bezpiecznej etykiety.
- Kosmetyki i farmacja: opakowania o niestandardowych kształtach, gdzie ważne są zarówno walory estetyczne, jak i higieniczne (często tamper-evident).
- Chemia gospodarcza: detergenty, środki czystości w oryginalnych butelkach, gdzie obkurczona folia idealnie podkreśla design i przekazuje ważne informacje.
Skontaktuj się z nami
Obkurczarki etykiet sleeve stanowią nieodłączny element profesjonalnych linii pakujących, w których priorytetem jest wyraźna identyfikacja produktu, przyciągający wzrok design oraz bezpieczeństwo (funkcja tamper-evident). Wybór odpowiedniego typu tunelu (powietrzny, parowy, IR czy hybrydowy), a także prawidłowe dostosowanie parametrów pracy (temperatura, prędkość, układ dysz) gwarantują uzyskanie doskonałego efektu końcowego.
Skontaktuj się z nami pod adresem kontakt@bovmatic.pl lub numerem 605 318 315, aby dowiedzieć się więcej o naszych usługach i produktach oferowanych przez naszą firmę i naszych Partnerów.
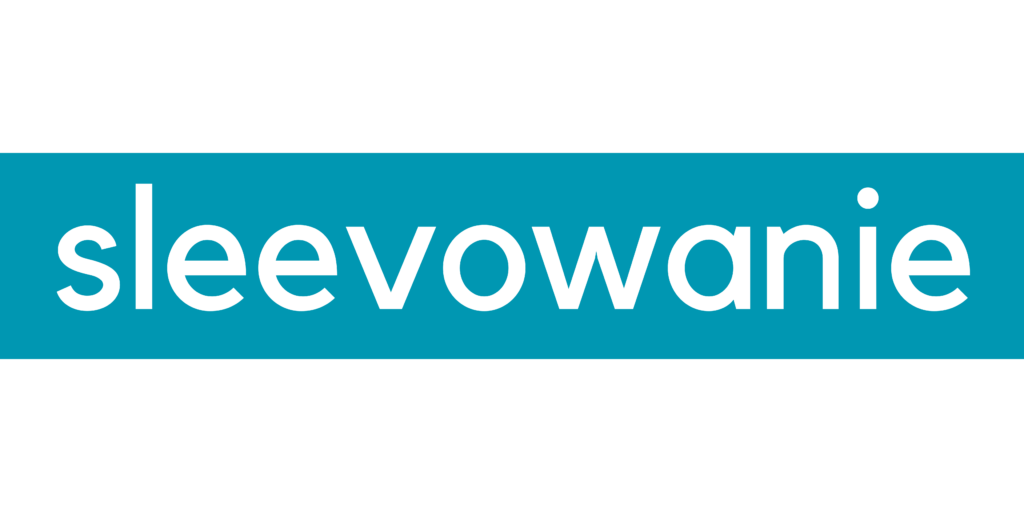